China's Manufacturing Facilities Reopen: Checklist for Best Practices During Coronavirus Outbreak
Share:
Welcome to Thomas Insights — every day, we publish the latest news and analysis to keep our readers up to date on what’s happening in industry. Sign up here to get the day’s top stories delivered straight to your inbox.
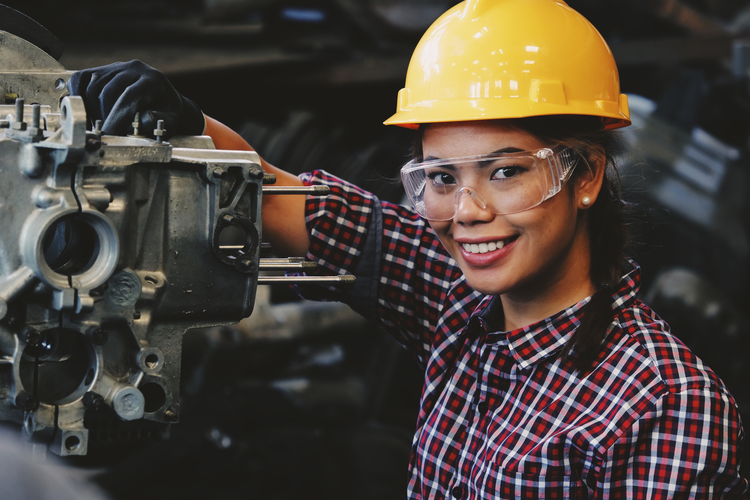
More than 60% of North American manufacturing companies say they’ve already felt the impact of coronavirus. Electronic manufacturers, for instance, are anticipating a minimum five-week shipping delay from suppliers.
(Download Thomas’ Coronavirus Survey Report for full coverage on the coronavirus’ impact on North American manufacturers and get daily updates on the latest news on how the coronavirus’ impact on shipping and logistics.)
Considering one in five of the manufacturing companies have production facilities in China, our team at the American Chamber of Commerce Shanghai gathered their insights regarding what needs to be done for Chinese facilities to resume operating procedure and output.
Since February 10, many factories in China have resumed some production, but most are not yet running at full capacity. Staff safety, compliance, manpower, and transportation issues continue to challenge companies even as customers and headquarters want increased output.
The COVID-19 outbreak crisis has created bottlenecks that vary from company to company, but this checklist outlines steps needed to support proper production.
Safety and Compliance
- Communicate with local government officials about the qualifications needed to operate.
- Requirements will differ from city to city.
- Most local and district governments will post regulations on their website or WeChat platforms.
- The municipal foreign affairs office for most cities has a hotline for foreigners to call for assistance on COVID-19 items.
- Maintain a source and supply of new PPE materials.
- E.g., surgical masks or respirators, gloves, sanitizer, infrared thermometers, etc.
- Implement conservative policies that improve morale and assure a safe, clean workplace.
- E.g., staggered lunch breaks, cleaning more often, regular temperature checks, etc.
Human Resources
- Clearly communicate risk assessment and expectations with all staff.
- Collect information from all staff members about current whereabouts and travel plans.
- Individually evaluate how soon each employee can return to the working location and pass quarantine.
- Account for a 14-day quarantine for staff returning from other cities.
- Have contingency plans for staff that are willing to return to work but face obstacles with transportation or accommodation.
- In some cases, providing private buses is a safer and faster alternative to public transportation.
- Consider providing temporary housing if local neighborhoods are not accepting returning migrants.
- Anticipate labor loss and proactively begin the rehiring processes.
Operating with Reduced Capacity
- Assess demand downstream and define your production goals.
- Domestic customers may not be fully operational either.
- Identify which products your customers prioritize.
- Generate a list of critical components.
- Take stock of available inventory and confirm warehouses are operational.
- Determine the skillsets of available staff and plan production accordingly.
Coordinating with Domestic Suppliers
- Confirm which suppliers are operational and understand their constraints.
- Discuss the productivity of tier-2 and tier-3 suppliers and evaluate the likelihood of fulfilled orders.
- Ask about their available inventory and confirm their warehouses are operational.
- Prioritize orders of critical components and establish realistic timelines.
- Establish payment terms that alleviate any cash flow concerns to promote suppliers running sooner.
- Consider low-interest loans in extreme circumstances.
- Research transportation restrictions between a supplier’s location and your facility.
- Plan for cost increases and delays for domestic freight and negotiate agreeable payment terms for delivery.
- In cases where critical components are impossible to obtain from current suppliers, seek new vendors.
International Transportation and Logistics
- Expect delays and communicate this to customers and suppliers. Reasons include:
- Blank sailings causing cancellations and global port congestion
- Lack of available domestic trucks for pick-up and drop-off
- Container build-up at Chinese ports
- Many warehouses in China are not fully operational
- Chinese customs officers are still working part-time, slowing customs release.
- Book as early as possible, for both air and ocean freight.
- Airfreight capacity has dramatically decreased.
- Price for ocean freight is expected to increase as production nationwide rises.
- Consider temporary changes in established Incoterms with your overseas partners.
- Agreeing to pay for the freight and being held responsible for its delivery can be a show of good faith.
- Negotiate flexible payment terms with your logistics service provider.
- A provider you have history with might be willing to extend credit during difficult times.
- In case of tight deadlines, ask your freight forwarder about premium options that guarantee space on vessels
- Carriers are expected to prioritize high-yield cargo in the coming weeks.
- Carriers can overbook vessels and offload non-premium shipments.
Download Thomas’ Coronavirus Survey Report for full coverage on the coronavirus’ impact on North American manufacturers. Also, get Live Updates here on the latest news on how the coronavirus’ impact on shipping and logistics.
About the American Chamber of Commerce in Shanghai
The American Chamber of Commerce in Shanghai (AmCham Shangai), established in 1915, was the third American Chamber recognized outside the United States. In China, it is known as the “Voice of American Business,” and it works to be the leading international business association in the country. The non-profit, non-partisan business association provides support, resources, and policy advocacy to its 3,000 members from 1,500 companies. Its mission is to facilitate those members’ business success while improving commercial ties between the U.S. and China, and it is devoted to the unrestricted flow of information, private enterprise, open markets, and free trade.
Image Credit: Image courtesy of StudioByTheSea / Shutterstock