Inside the iPhone: How Apple Sources From 43 Countries Nearly Seamlessly
Share:
Welcome to Thomas Insights — every day, we publish the latest news and analysis to keep our readers up to date on what’s happening in industry. Sign up here to get the day’s top stories delivered straight to your inbox.
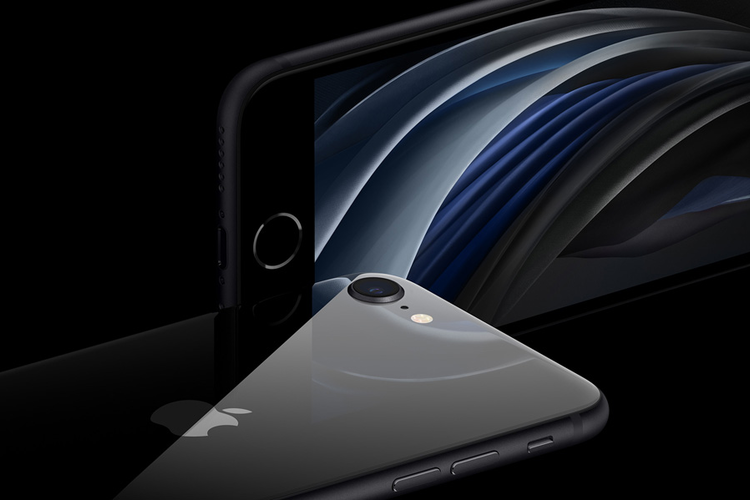
Ever since Apple introduced the iPhone in 2007, the multinational company has consistently edged out its competition with its extensive but efficient supply chain processes.
Although most famous for its tech innovations and high-quality product, Apple’s supply chain strategies are just as much a reason for the company’s long-standing success. Even more so is Apple's supply chain designated for its iPhones; the strategy has to handle completely new products nearly every year and skyrocketing demand during release.
Designed in California, Made Around the World
Though the company’s industrial designers are located in Apple’s headquarters in Cupertino, California, Apple largely depends on overseas manufacturers for ready-made product components and assembly.
The company designs the iPhone in California, purchases components from suppliers in 43 countries across six continents, sends the parts to factories to be assembled, and then ships completed iPhones to warehouses and then to retailers around the world.
As overseas labor rates increase, Apple has moved some business back to the U.S. to lower the total cost of ownership. But it still sources components from a wide range of suppliers around the world.
The iPhone is made of hundreds of individual parts, each manufactured by different suppliers. For example, parts of the iPhone camera and glass screen were built in Japan, elements of the battery were built in China, and the accelerometer—which tracks the phone’s acceleration and enables geographic orientation – was built in Germany.
Companies looking to strengthen their supply chains—a major focal point as COVID-19 continues to affect virtually every industry worldwide – would be wise to carefully assess all outsourcing and onshoring possibilities. As the iPhone disruption has shown, relying too heavily on overseas manufacturing can pose challenges when faced with major disruptions or crises.
Minimized Inventory, Maximized Efficiency
Because Apple makes so many iPhones each year, an overload of supplies is typically not an issue. In fact, component shortages have threatened to slow the supply chain during the years Apple announces new iPhone models.
But the company has found ways to make the iPhone supply chain as efficient and cost-effective as possible, reducing the need to keep surplus products in storage. For companies looking to streamline their own inventory management processes—particularly those in the tech-device sector – the iPhone model may offer useful guidance.
By treating devices as if they had an expiration date, Apple is able to better meet spikes in demand when new products are launched – cutting down on waste and allowing them to remain as nimble as possible.
“When Tim Cook initially took over Apple’s supply chain, he cut down the number of component suppliers from 100 to 24, forcing companies to compete for Apple’s business," writes Sam Oliver at Apple Insider. "He also shut down 10 of the 19 Apple warehouses to limit overstocking.”
Although Cook’s strategies have proven successful over the years, COVID-19 dealt a blow to the iPhone supply chain. With many suppliers located in hard-hit China and parts of Europe, disruptions have been widespread –with smartphones particularly vulnerable, as they require a lot of human labor as well as many outsourced parts.
As recovery continues, one China-based iPhone maker, Foxconn Technology Group, announced in late March that it has found enough workers to allow its plants to meet seasonal demand.
Strategized for the Future
Over the years, Apple has launched a number of programs to combat the toll that smartphone manufacturing takes on the environment, with the ultimate goal of using only recycled materials in its products – eliminating the need for material mining. The company currently uses 100% recycled tin in the logic boards of its newest iPhones.
According to Apple’s 2019 Environmental Responsibility Report, covering the 2018 fiscal year, “The A11 and A12 chips used in iPhone 8, X, XS, XS Max, and XR allow more processing power to be packed into smaller silicon dies, which reduced Apple’s 2018 carbon footprint by 160,000 metric tons.”
These chips, which are outsourced to China, Taiwan, and the Philippines, act as performance and efficiency cores, allowing for 15% faster iPhone performance and 40% less power consumption.
Apple has also found a way to cut the carbon footprint of each product by almost 50% – a major feat considering 60-70 elements from the periodic table are used in the average smartphone. Because standard recycled aluminum accumulates impurities every time it’s recycled, Apple engineered an alloy that can accommodate scrap sources of aluminum while providing the same durability, strength, and quality finish.
Apple’s initiatives to make iPhones more sustainable have become increasingly important in recent years as the majority of today’s consumers expect the companies they buy from to commit to social and environmental sustainability efforts.
COVID-19 and the Next iPhone Launch
As the COVID-19 crisis continues to alter supply chains across the world, Apple is focused on ensuring its iPhone supply chain weathers the storm.
Rumors continue to circulate regarding the fate of the next iPhone model—the iPhone 12, the first of Apple’s smartphones to offer 5G capabilities – slated to launch in early fall. Many suppliers are predicting a delay due to potential challenges with final testing in China, despite the fact that the tech giant has successfully built the necessary test models.
Going forward, Apple – along with countless other businesses – will likely be taking this supply chain disruption as an opportunity to identify areas for improvement, further strengthening the company’s adaptability and agility to help ensure a strong competitive edge.
Image Credit: Courtesy of Apple