Reshoring Advantages and Disadvantages
Share:
Welcome to Thomas Insights — every day, we publish the latest news and analysis to keep our readers up to date on what’s happening in industry. Sign up here to get the day’s top stories delivered straight to your inbox.
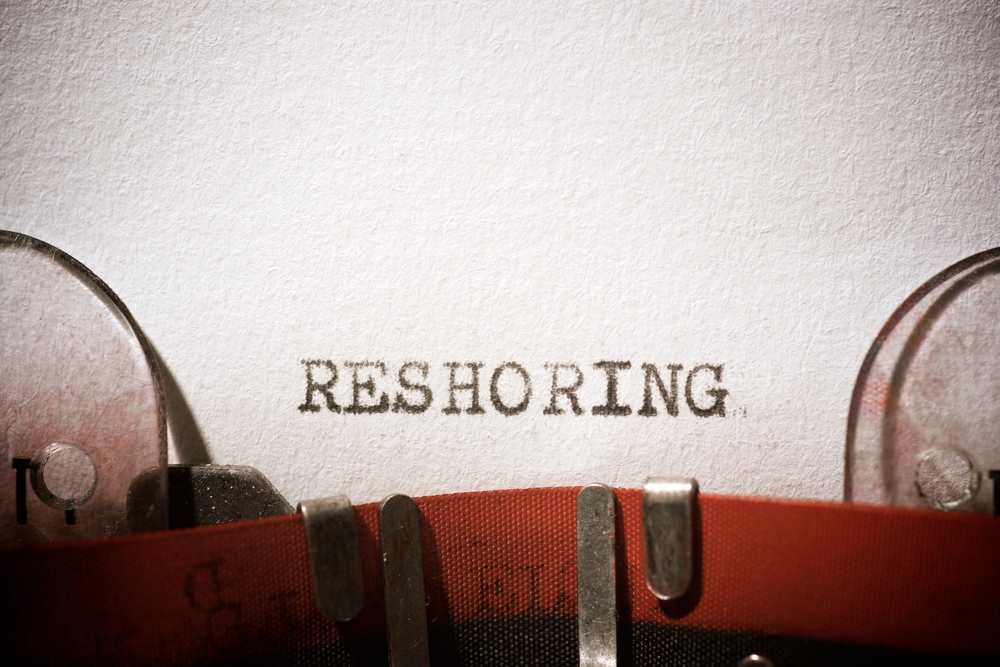
Reshoring brings manufacturing operations back to a company’s country of origin and offers several advantages in the global supply chain and manufacturing industry. In recent years, reshoring has gained significant attention as companies reevaluate global supply chains and production strategies amid ongoing disruptions.
Reshoring aims to reverse the previous trend of offshoring, where companies sought cost advantages and expanded operations to foreign countries. However, there are also a variety of disadvantages to reshoring. From higher initial costs to skills gaps, this article does a deep dive into the advantages and disadvantages of moving production back home.
Advantages of Reshoring in Supply Chain and Manufacturing
By shifting production closer to the domestic market, companies can experience cost savings, improved quality, and shorter lead times, positively impacting job creation, innovation, and responsiveness to market demands.
1. Cost Savings
Reshoring can lead to significant cost savings in the long run. While offshoring to a foreign country initially presents lower labor costs, rising wages in traditional offshore manufacturing destinations and increasing transportation and logistical expenses have eroded this advantage.
By reshoring, companies can reduce shipping costs associated with long-distance shipping, import and exports, and inventory holding. Additionally, proximity to suppliers and customers can lower transportation costs and provide opportunities for just-in-time manufacturing, further reducing inventory carrying costs.
2. Improved Quality Control for Manufacturing Operations
Switching to domestic manufacturing enables enhanced quality monitoring throughout the production process. Direct oversight and increased proximity allow for real-time tracking, faster identification of defects or issues, and immediate corrective actions.
Manufacturers can implement stringent quality procedures, conduct regular inspections, and communicate better with the production team. This focus on quality at the manufacturing facility can result in higher customer satisfaction, increased brand reputation, and reduced product recalls or returns costs.
3. Shortened Lead Times
Reshoring shortens lead times in procurement, manufacturing process, and sales cycle, improving responsiveness to market demands. Companies can reduce order cycle times and enhance speed-to-market by eliminating the need for lengthy overseas transportation.
Shorter lead times enable more flexibility in production planning, allowing businesses to quickly adapt to changes in customer preferences, market trends, or unforeseen events. This agility provides a competitive advantage by enabling faster product launches, reducing stockouts, and meeting customer demand and expectations for timely delivery.
Disadvantages of Reshoring in Supply Chain and Manufacturing
While reshoring offers various advantages, evaluating the potential disadvantages and challenges associated with a significant strategic shift is essential.
1. Higher Labor Costs
One of the primary challenges of reshoring is the potential for higher labor rates compared to offshore locations. The number of skilled workers or the amount of skilled labor also factors into the labor rates.
The practice of offshoring often sought lower labor rates by leveraging cheaper labor markets. By bringing production back home, companies may face higher wages and benefits expenses, which can impact profitability, especially in labor-intensive industries.
However, tax cuts from state and local governments can offset higher costs when corporations create jobs and use domestic suppliers. Automation technology also helps reduce costs when reshoring manufacturing operations.
2. Infrastructure Limitations
Reshoring specific industries may be constrained by infrastructure limitations in certain regions. Offshore locations may have developed specialized infrastructure, production facilities, and manufacturing ecosystems that are not readily available or cost-effective in the home market.
For example, industries relying on advanced technology, specialized equipment, or technical expertise may face challenges when attempting to reshore. Companies need to assess the availability and cost-effectiveness of the required infrastructure, including transportation networks, energy supply, and supporting services, to ensure the viability of reshoring efforts.
3. Supply Chain Disruptions
Reshoring can introduce initial disruptions in the supply chain. Transitioning production from offshore locations back to the United States may involve complex logistical challenges, including the need for new supplier relationships, the re-establishment of local supply chains, and adjustments to inventory management.
Additionally, the initial phases of reshoring can result in temporary disruptions in production, potentially impacting customer orders and delivery schedules. Careful planning, risk assessment, and effective communication with suppliers and customers are crucial to minimize disruptions and maintain continuity during the reshoring process.
4. Regulatory and Compliance Factors
Reshoring may also introduce additional regulatory and compliance factors that businesses must navigate. Offshoring production often benefits from specific tax structures, trade agreements, and regulatory frameworks that might differ when operating domestically.
Companies must assess the regulatory environment, compliance requirements, environmental regulations, labor laws, and safety standards. Complying with these regulations may entail additional costs and administrative efforts, which should be carefully considered when evaluating the benefits of reshoring.
Factors to Consider in Reshoring Decision-Making
Choosing to reshore involves carefully evaluating multiple factors to determine the return on investment and other benefits of bringing manufacturing operations back home.
Organizations should consider various aspects beyond the cost of labor, including conducting a comprehensive total cost analysis, assessing the proximity to the market, and addressing intellectual property (IP) protection and local regulations.
1. Total Cost Analysis
Beyond labor and material costs, organizations should conduct a comprehensive total cost analysis. While labor costs are important, businesses must also evaluate other cost factors such as shipping costs, inventory management, taxes, regulatory compliance, and currency fluctuations.
By assessing the total cost of production, companies can gain a more accurate understanding of the financial implications of reshoring and identify potential cost savings in the long run.
2. Proximity to Market
Being closer to the market customers is a significant advantage of reshoring. Reduced transportation costs and shorter lead times improve supply chain efficiency and responsiveness. Proximity allows for faster delivery of products, reduced inventory carrying costs, and increased flexibility in adapting to market demands and fluctuations.
Organizations can better understand customer needs, preferences, and changing trends, enhancing customer satisfaction and increasing market competitiveness.
3. Intellectual Property Protection
Reshoring often offers more substantial IP protection than offshore locations. Many countries have robust legal frameworks and enforceable IP rights, providing a more secure environment for businesses to safeguard their proprietary technology, designs, and trade secrets.
Protecting IP is vital for maintaining a competitive edge, fostering innovation, and preventing unauthorized replication or counterfeiting.
4. Local Regulations and Compliance
Organizations must consider local regulations and compliance requirements when reshoring.
Countries have varying legal frameworks, tax policies, labor laws, environmental regulations, and safety standards. Businesses need to assess the impact of these regulations on their operations and understand the associated costs and administrative requirements.
Compliance with regional laws is essential to avoid legal problems, maintain a positive reputation, and ensure a smooth transition during the reshoring process.
5. Supply Chain Resilience and Risk Management
Reshoring decisions should account for supply chain resilience and risk management. While reshoring can lower risks associated with long and complex global supply chains, it can also introduce unexpected risks and challenges.
Organizations must assess potential risks, identify mitigation strategies, and establish contingency plans to address disruptions, supplier dependencies, geopolitical factors, and unforeseen events. A well-planned risk management approach ensures operation continuity and minimizes potential disruption impact.
Is Reshoring Right for You?
Reshoring decisions require a comprehensive evaluation of multiple factors beyond labor and material costs. Organizations should conduct a total cost analysis, assess the advantages of proximity to the market, consider IP protection, and address local regulations and compliance requirements.
By carefully considering these factors and conducting thorough assessments, businesses can make informed reshoring decisions that align with their strategic objectives, optimize efficiency, and enhance competitiveness in the domestic and global markets.
More Reshoring Insights
- Reshoring vs. Nearshoring: Differences and Similarities
- What Is Reshoring, and Why Do Companies Reshore?
- Friendshoring: Definition, Benefits, and Key Characteristics
- Offshoring vs. Outsourcing: What's the Difference?